by Harry Moser, Founder/President, Reshoring Initiative
Tectonic shifts in global supply chains were apparent even before the COVID-19 outbreak. Analysis by Bank of America points to tariffs, automation, carbon footprint issues, and national security as driving factors of the shift.[1] The Reshoring Initiative’s 2019 Data Report, due to be released in May, adds rising offshore wages and increased recognition of a broad range of costs and risks. Geopolitical turmoil and shifting priorities had made far-flung supply chains less appealing. The COVID-19 precipitated shock to our hyper-connected global supply chains was systemic and paralyzing. The coronavirus crisis revealed clear evidence of our overdependence on imports, especially from China. Companies have begun to reevaluate their supply chains and consider reshoring.
The increased credibility of reshoring or not offshoring is highly relevant to engineering management. Harvard Business School’s Professors Pisano and Shih have clearly described how the industrial commons is depleted when manufacturing is offshored. Both engineering and manufacturing suffer from the separation. There is also a tendency to overcome the problem by having engineering follow manufacturing to low labor cost countries.
Import Overdependence
The COVID-19 outbreak has made Americans keenly aware of our overdependence on imports of medical devices and pharmaceuticals. According to the Department of Commerce, 97% of all antibiotics in the U.S. come from China.[2] U.S. manufacturers source 80% of their active pharmaceutical ingredients (APIs) overseas, primarily from China, and China is the chief supplier of APIs for producers in other countries. Eight-six percent of U.S. hospitals and healthcare systems are concerned about personal protective equipment (PPE) shortages for frontline medical workers.[3] However, about 80% of all PPE is manufactured in Asia.
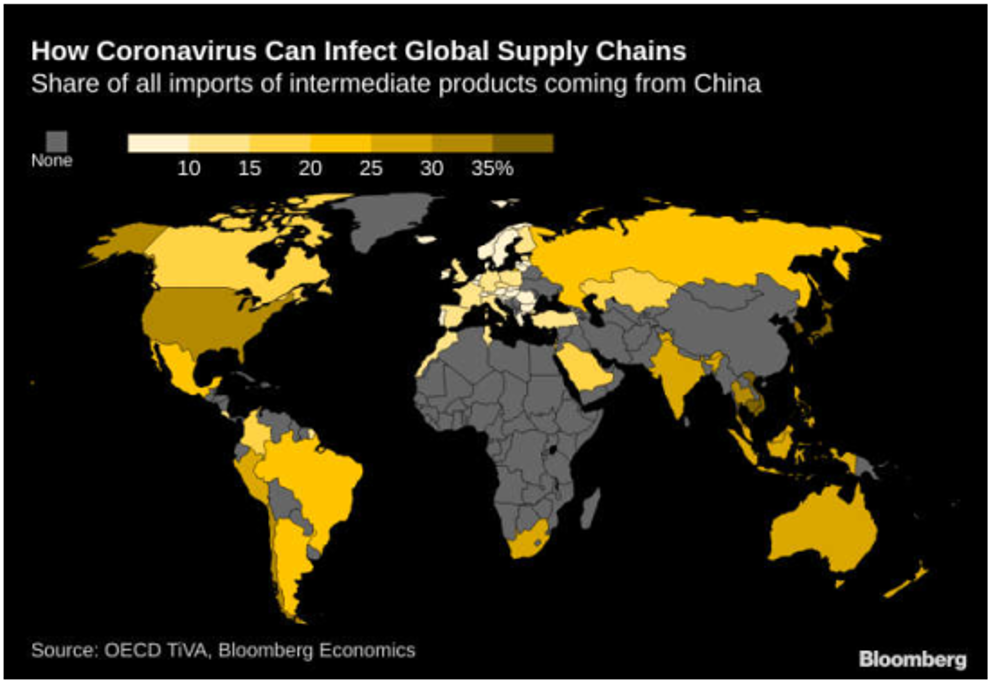
Impact on Supply Chains
A recent report by the United Nations Conference on Trade and Development said, “the COVID-19 outbreak will potentially accelerate existing trends of decoupling and reshoring driven by the desire…to make supply chains more resilient.”[4] According to a Thomas study, 60% of U.S. manufacturers say business has been impacted by the coronavirus.[5] A recent Thomas follow-up study found that over 50% of manufacturers surveyed are ‘likely’ to ‘extremely likely’ to bring production and sourcing back to North America post-coronavirus. Additionally, 47% of U.S. manufacturers report they are now seeking domestic sources of supply.[6] The Reshoring Initiative can provide resources to evaluate if reshoring is right for your company.
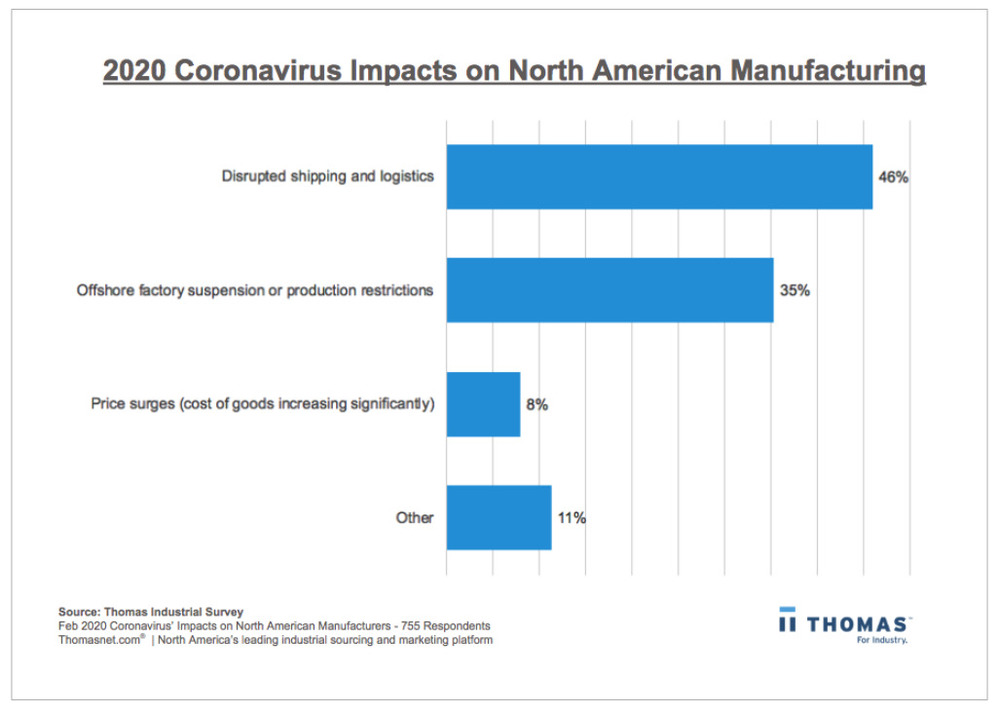
Trade Data
Trade data shows a decline in Chinese shipments that began in mid-February 2020 as the coronavirus outbreak caused Chinese factories to shutter. Key U.S. medical shipments from around the world slowed during the crisis. Hand sanitizer and swab imports from China dropped by 40%, and N95 mask imports were down 55% in March 2020.[7] As Chinese factories slowly reopened, export restrictions were enforced due to quality issues and China’s need to fill their own domestic demand. Critical medical supplies were stranded as suppliers and brokers were unable to receive official clearances for U.S. bound shipments.[8]
Use TCO for the Offshoring/Reshoring Decision
A broad range of costs and risks can be quantified using the free online Total Cost of Ownership Estimator®. Making sourcing decisions based solely on price often results in a 15% to 25% understatement of offshoring costs. TCO analysis helps companies objectively quantify, forecast and minimize total cost. It takes into account the Ex Works price plus 28 additional costs and risks. TCO quantifies factors, such as those associated with the risk of supply chain shocks or disruptions caused by natural disasters, political unrest or even pandemics. Use of TCO breaks down internal silos, making the impacts on sales, inventory, warranty and engineering relevant to the sourcing decision. Recommended reading includes “Getting A Company Started with TCO” to plan your TCO analysis.
About the Author
After leading GF AgieCharmilles for 25 years, Harry founded the Reshoring Initiative to bring five million manufacturing jobs back to the U.S. Largely due to the success of the Reshoring Initiative, Harry was inducted into the Industry Week Manufacturing Hall of Fame 2010, participated actively in President Obama’s 1/11/12 Insourcing Forum at the White House and is on the Commerce Department Investment Advisory Council. Harry is frequently quoted in the WSJ, NYT and Forbes, and seen on Fox Business, MarketWatch, and other national TV and radio programs. He received engineering degrees at MIT and an MBA from U. of Chicago.
Apply for a National Reshoring Award
National Metalworking Reshoring Award Companies that have successfully reshored metal-worked products, parts or tooling, including castings, are invited to compete for the National Metalworking Reshoring Award. The Reshoring Initiative, PMA, NTMA, and AMT are pleased to sponsor this competition. Applications must be submitted by June 30, 2020. To view award details and enter to win, visit www.amtonline.org/reshoringaward. OEMs and contract manufacturers are both eligible. FDI (foreign direct investment) is also eligible. AMT and the Reshoring Initiative are also focused on helping companies make the right sourcing decisions: Rebuilding the Domestic Supply Chains.