by Jerry Westbrook, PhD, FASEM, Professor Emeritus - University of Alabama at Huntsville
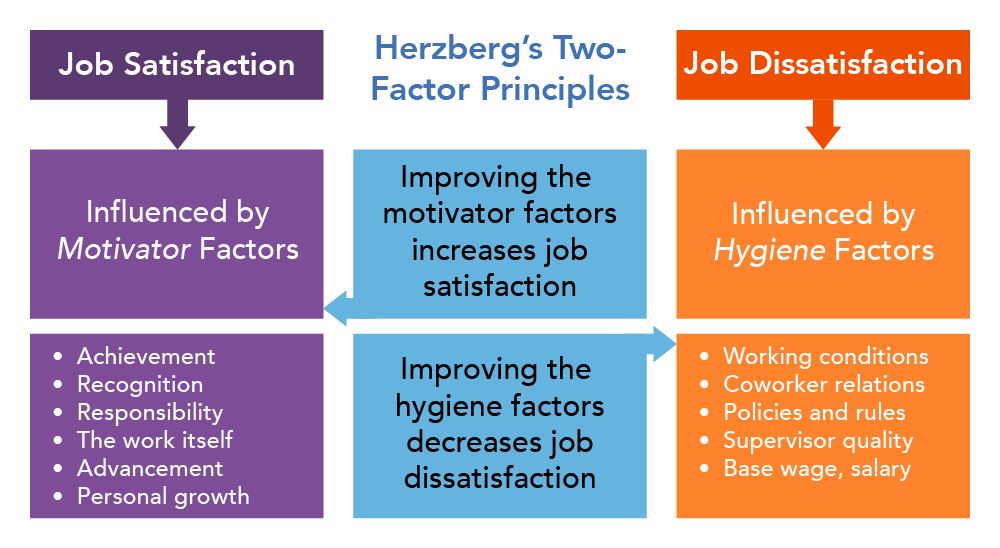
This is the second article on applications of the Guide to the Engineering Management Body of Knowledge. The primary contribution of these articles is how the EMBOK can guide the technical manager in applications. The material discussed is from Domain 2. If a practitioner focuses on Domain 2, he or she can have a successful career in technical management. The other domains in the EMBOK complement the first and second domains but primarily the second. This conclusion comes from my experience as well as many colleagues’ experiences in applying the concepts contained in the EMBOK.
The topic of the day is Herzberg’s Motivator-Hygiene Concept (EMBOK 2.3.3.) Dr. Herzberg did a study of engineers and accountants to determine the factors associated with motivation and de-motivation. Any manager should have a good idea of those things that tend to motivate employees. They should also understand those issues that cause the opposite reaction. Most managers assume that they know these things instinctively. According to Herzberg’s research, most of these assumptions are incorrect.
Herzberg’s research found that one set of factors were associated with motivation and another set associated with de-motivation. He called the factors associated with motivation as motivators. They are, in the order of responses from subjects in the study:
- Recognition
- Achievement
- Advancement
- Responsibility
- The job itself
The de-motivators we called hygienes because they were associated with the work environment, not the work itself. They are:
According to this research, the motivators were only positive and the second group, the hygienes, were only negative. The highest motivational value of any hygiene is zero. If company policies are the best in the industry, they have zero motivation. If these policies are perceived to be unfair to one employee or to a group, they are perceived negatively.
It must be noted that managers have more control over motivators but they are difficult to administer. Hygienes do not lead to motivation but their improvement can be expensive to the company.
The following case involves an attempt to make motivators out of hygienes. Many organizations make similar efforts with similar results.
Motivation Gone Awry
“First Fiber Glass” Company asked me to assist them in increasing their productivity and product quality. It was quickly determined that employee turnover at critical operator positions were running approximately 40% per year. The operator jobs required a great deal of agility and hand-eye coordination. The job could be dangerous as it was working with molten fiber glass at 2000 degrees C. Management relations with the union turned contentious while I was there. I was working closely with union employees attempting to make the job safer and more productive. Seeing my positive relationship with some workers, management asked me to convey a message to the union. They asked me to ask the union if they had concerns that management could address to show good faith effort to work more effectively with them. Realizing that the union would likely focus on hygienes, I suggested that management should focus on more opportunity and advancement potential for workers. Management told me that they had discussed matters and wanted to pursue the plan as explained.
I met with union leaders and explained management’s desire to demonstrate good faith. The leaders quickly pointed out that the plant floor had a buildup of binder over one inch thick. Binder is sprayed onto molten glass fibers to give them tensile strength. Some of the binder actually coats the glass fibers. The remainder falls to the floor where it accumulates. They pointed out that the binder buildup was unsanitary and unsafe and that it should be removed. I went back to management with the union response. Management was aware of the situation and readily agreed with the union’s assessment. They decided to shut the plant down for a week and remove the binder buildup. Workers were not laid off. They either participated in training or the cleanup effort. The binder had to be chipped up with power equipment. The Research and Development group suggested that a new epoxy paint might prevent the buildup from developing in the future. After the buildup removal, the plant floor was painted with a pastel green epoxy paint. Normal operations were restarted the next week.
Management asked me to meet with the union to gage the response to the cleanup effort that the union had suggested. In the meeting with the union, they readily expressed appreciation for management’s efforts to clean up the plant. They were, however, quick to point out that their shower room was in need of major repairs. The shower room was the first thing workers saw when they came to work and the last thing they saw when they left. Broken fixtures were symbols of how the company viewed its employees. They were seen to be an indication that workers were not important to the company. I brought that message back to management. Again, they agreed with the union and had the shower room completely refurbished.
Once more, hoping that the union could see that management was conciliatory, management asked me to meet with the union. The union officers were very appreciative of management’s actions. They did point out that the employee parking lot was in a state of disrepair. There were many potholes large enough to damage their cars. Again, this was their first connection with the employer when coming to work and the last before leaving work. Of course, I brought their parking lot concern to management. They readily agreed to repave the parking lot and instructed me not to meet with the union leaders again.
The union’s list of hygienes exceeded management’s resources. Management finally saw that they were not getting productive results by addressing non-production issues. Later, they did agree to open new training and lead classifications in the production departments with the greatest opportunities for improvement. This was well received by the union. Productivity, quality and morale did increase. Little connection was observed between the response by the union to these motivators and the long list of hygienes. Management was glad that production and quality had both improved and did not seem to get the connection of applying motivators when the long list of hygiene applications failed to achieve positive results.
Summary of Herzberg’s Advice
Do the best you can with hygienes. You won’t get motivation but you will avoid serious problems. Significant long term improvements in motivation are achieved through focus on motivators: recognition, achievement, possibility of growth, advancement, responsibility and the job itself. It is counter-intuitive for a manager to respond to a request for a hygiene improvement with an analysis of the status of motivators but that is what must be done, after the hygiene request is investigated and acted on.
About the Author
Dr. Westbrook has served the American Society for Engineering Management in a variety of positions. He is a past President of the society, past Executive Director and an ASEM Fellow. He founded ASEM's program to certify master's degree programs that meet ASEM program standards. He was instrumental in the founding of a master’s program in EM at the University of Tennessee and the master's and Ph.D. in engineering management at the University of Alabama in Huntsville.
His research and teaching focuses on behavioral concepts in management and the challenges of managing knowledge workers. Dr. Westbrook received his Ph.D. degree from Virginia Tech in Industrial Engineering and Operations Research, master’s degree from the University of Tennessee in Industrial Engineering and a B.E. from Vanderbilt in Electrical Engineering. In addition to ASEM, he is also a member of ASEE, IIE, and NSPE. Dr. Westbrook authored or co-authored 20+ refereed papers on engineering management topics. Dr. Westbrook has developed a series of seminars on managing knowledge workers. He and a team of talented professionals have delivered these seminars to a variety of clients in several states.