By Donald Kennedy, P.Eng.
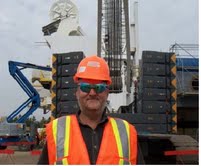
A huge problem that is seldom discussed and maybe even often not recognized is the tendency for many engineers to over design. The thinking is that more is better, but sometimes adding too much makes a situation worse. It is difficult to personally take the responsibility for cutting back on a design but in a competitive environment these decisions may save a company.
I am going to relate an example where over design had been taken to an extreme. I had to champion a project to handle steam condensate in a process plant. This was basically distilled water that came off the system and was collected in a tank. There were nine such tanks at the plant. The company was paying $4 million dollars a year to have the water trucked off site. The filling of the tanks was not uniform nor predicable and a truck and driver were paid to be on hand 24 hours a day 7 days a week to empty any tank that was full. However, the proposed project to automate the pumping of the water back into the process was $8 Million, making it difficult to raise the capital to eliminate the need for the truck to be on standby.
When I became the champion of the pump project, I was told that each tank held 380 barrels. Although the tanks filled at unpredictable rates, I was told that the tanks were sometimes emptied twice a day. To assure the tanks would not overflow, the proposed pumps were sized at 80 gallons per minute (gpm) in the $8 million dollar project. The water needed to be injected at a high pressure on the discharge side of a pump.
First off, I realized that a 380 barrel tank is 16,000 gallons. It would take 200 minutes to completely empty this tank at 80 gallons a minute. That is a little over 3 hours. When I talked to the process engineer, he said that he was given 40 gpm as the needed rate. There was a common pump that could do that, but he was nervous that he might need a little more, so to be safe he went to the next larger common size. When I went to the operations person that provided the 40 gpm rate he said he calculated that 22 gpm was needed but the common pump that could easily handle it was the 40 gpm size. Each person had built in a buffer.
By this time, I figured I better confirm how the 22 gpm rate was derived. This was based on the assumption that the 380 barrel tank was emptied twice a day. When I went to the truck driver, he stated his truck held 60 barrels. Because the fill rate was unpredictable, operations would notify him to empty a tank whenever it was half full to assure it would not overflow. So the maximum volume emptied was 120 barrels in a day, not 760. That is 3.5 gpm (and I will not round up to 4 to be safe) compared to the 80 gpm being designed for. I also discovered by checking the process data, that only half of the tanks had to be emptied more than once a week. I also checked with the environmental group and they confirmed that if the condensed steam overflowed out of a tank, it was basically just distilled water and no negative environmental impact would result, nor would any regulatory reporting be necessary to account for water being on the ground. By selecting pumps 1/20th the size and only installing them on half the tanks, the $8 Million project shrank to $2 Million. That is now a 6 month payback and much easier to raise the capital for. If any tank was filling up, a truck could be ordered to empty it and if the truck was late some water would be released onto the ground.
A manager without the engineering background may not feel comfortable challenging the assumptions made in the original proposal. This becomes another example of the value of the Engineering in Engineering Management.